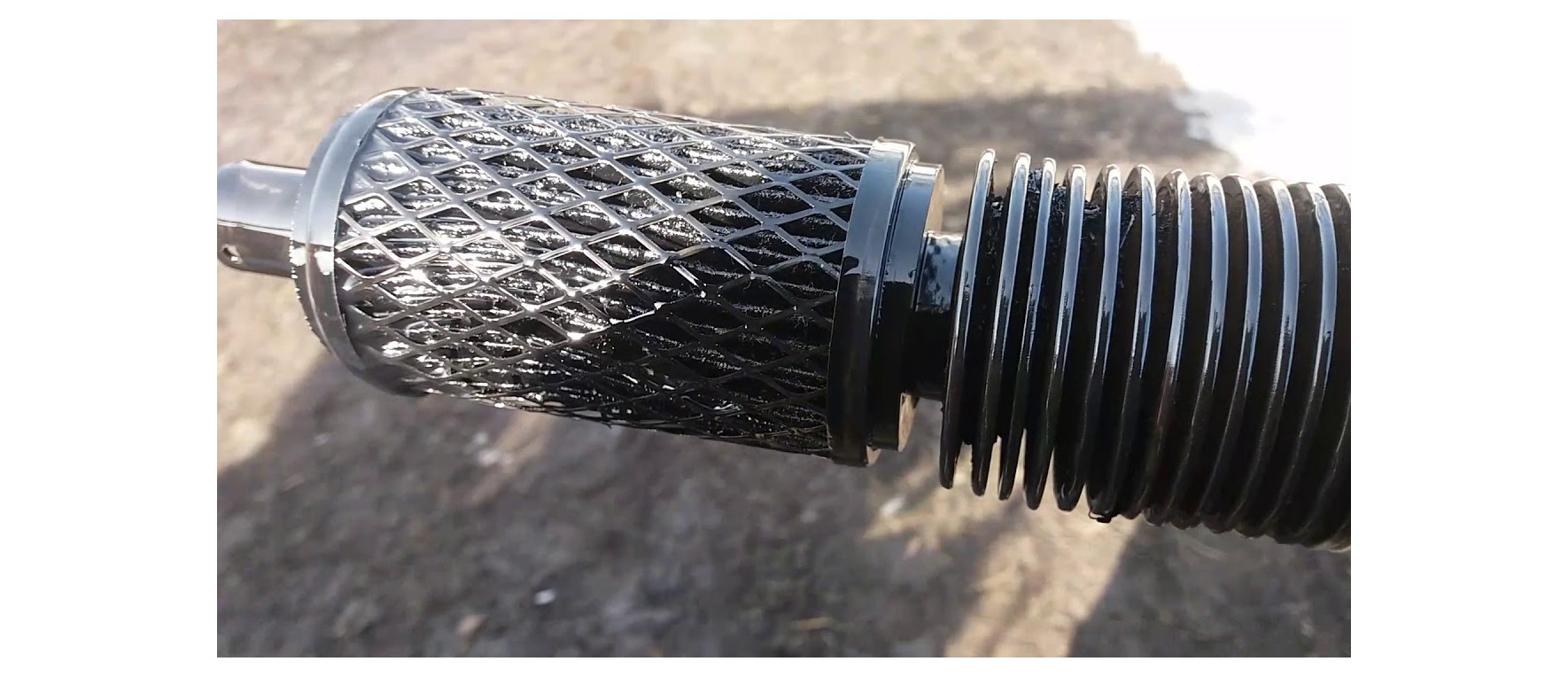

Hydraulic system of heavy trucks, off-road vehicles, agricultural and construction machines, cars and equipment depends on the quality of the hydraulic fluid and, consequently, its qualitative filtration (cleaning). In order for the hydraulic system to work with maximum efficiency, it is necessary to reduce to the absolute minimum substances contaminating the hydraulic fluid - this is not difficult if you use high-quality hydraulic filters.
Hydraulic filters are indispensable components of hydrosystems, which operate in particularly difficult conditions and are constantly subjected to extremely high load. The quality of work depends on the operational properties of the hydraulic oil, as well as on the reliability of the components of the hydraulic equipment themselves (seals, actuators, pumps, valves). All these parts undergo erosion, permanent erosion, high pressure impact.
Filters of this type serve as protection of hydraulic systems of engineering from particles of dust, oxides, condensate, rust, fibers, paints, sealants, metal particles formed as a result of the friction of hydraulic parts and contribute to reducing the wear of the mechanisms. Thanks to the filters it is possible to continue the work of valves and pumps, to avoid the jamming of electric valves, the occurrence of scratches on plunger pairs.
Usage
Areas of use of hydraulic filters include:
- hydraulic drives of transport and construction machines, mechanisms and devices of aviation engineering, machine tool and lifting and transport equipment;
- hydraulic amplifiers of industrial equipment and road engineering;
- stamping and press production;
- drilling equipment, logging equipment;
- compressors and transformers;
- hydraulic systems and equipment in refineries, chemical, mining and machine-building enterprises, food industry and packaging.
Structure
In a standard version, the hydraulics filter consists of a housing, a filter element, an indicator of pollution, a bypass valve (possibly absent). The outer casing can be made of different materials: aluminum, stainless steel or durable plastic. Everything is connected with conditions and temperature. Production of filter elements of hydraulic filters is carried out using raw materials of different types.
There are several main types of materials from which the filtering element is made:
- mesh (the filter core is a grid of thin stainless steel, the overall dimensions of which are very small. These filters are capable of separating only large particle sizes. Thus, they are mainly used as filters of pre-filtration. This advantage is the possibility of regeneration (recovery), which allows the use of a hydraulic filter for cleaning of washing liquids and filtration of waste liquids. Net filter flanges are manufactured with a filtration rate of 10 to 250 microns);
- cellulose (filtering elements from cellulose are characterized by a rather high degree of filtration, but are not very durable. Typically, hydraulic filters with cellulose are installed on equipment which is more often passed technical inspection);
- fiberglass (durable and effective, have an increased rate of absorption of dirt, they are 4 times longer, these hydraulic filters have a filtration rate of 3 μm to 60 μm).
The filter material for the manufacture of a hydraulic filter can be one-time (paper and inorganic fiberglass) or renewable (metal mesh).
The fill indicator will show you how dirty the filter is (not present in all models). It allows to understand when a replacement is needed. If it does not, follow the manufacturer's recommendations. It is advisable to replace before the bypass valve opens. The bypass valve is not available in all hydraulic filters. It performs the function of passing oil through the filter at the highest pressure.
So, the kit of high-quality hydraulic filters is:
• Case made of stainless steel, aluminum, steel;
• Single or multiple filter (best if the filter element is made of metal, cellulose or fiberglass);
• availability of a fill indicator;
• Bypass valve (it is not in all filters, but in its absence, the filter can burst, and all dirt will appear inside the system).
Types
Filters for hydraulic systems differ in the following types:
- suction (install in front of the pump and use for the selection of large particles);
- pouring (provide high-quality cleaning of liquid from small particles that can get during filling the tank);
- pressure or high pressure (set in the pressure line after the pump and in front of the electric valve to protect the valve plunger from the mechanical impurities present in the hydraulic fluid, used for deeper filtration, protect high-sensitivity components of the system, characterized by high structural durability, ease of installation, the presence of an indicator of pollution level);
- slit (remove microparticles of contaminants during the passage of the working fluid through the cleavage of the element);
- drain or return (set before the drain of oil in a tank and used for the perfect oil purification, which passed the entire hydraulic process. They serve to remove from the working fluid fractions that appear in the process of wear of the device (products of oxidation and disintegration of oil, rust). Designed specifically for heavy duty mobile machines and industrial plants, drainage filters are manufactured with a filtration rate of 10 μm, 25 μm, 60 μm and 125 μm.
There are also special bypass hydraulic filters, which help to clean the liquid before entering the hydraulic system. It is necessary to pay attention to the location of the filters. There are technical recommendations, but the most important is the availability of its removal, cleaning, washing or replacement.
Filters such as SPIN-ON can be installed in low pressure, high pressure and return lines. Variable hydraulic filter elements, screwed on the filter head. This allows change the filter elements very quickly.
SPIN-ON filters are specifically designed to control pollution in hydraulic and lubricant circuits for mobile and agricultural machinery.
Due to the peculiarities of the construction device, the installation site, the purpose of the hydraulic filters are divided into:
- partial flow (the filter is installed in parallel with the system of supply of hydraulic oil, therefore only part of the working fluid passes through it.This type of hydrosystem has a low efficiency), full flow (the filter element is contained directly in the hydrosystem, so all the working fluid passes through it. This type of connection must have a bypass valve that is mounted inside the filter itself or in its housing), combined (include the properties of both systems. This approach ensures the highest efficiency of cleaning the hydraulic oil) - (depending on the volume of fluid passing through the filter);
- lattice, slit, superficial (in connection with the design features);
- suction, pressure, drainage (at the place of installation, respectively: on the suction pipe, after the injection pump, between the working mechanisms and the liquid reservoir).
Recommendations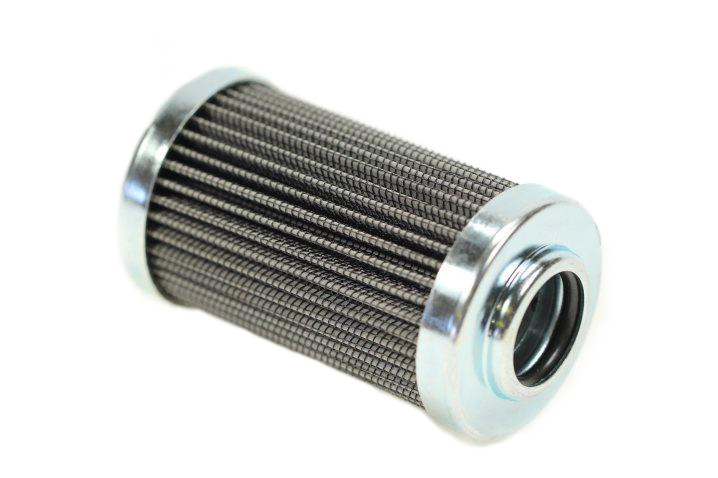
Before buying a hydraulic filter, you need to consider:
- what liquid it will clean,
- where it will be installed,
- what purity of oil is needed at the output
- possible temperature
- the limit of pressure
- size.
To reduce the risk of a breakdown, only high-quality devices should be used. Popularly used hydraulic filters of the world-famous brands: DONALDSON, MANN, FILTREC, HYDAC, PARKER. They need to be changed periodically, otherwise there may be problems.
It is recommended to consult a specialist who will help you to take into account all the nuances when choosing a hydraulic filter for your equipment. We advise you not to save because, with a poor selection, you will have to spend more money.
By materials of Internet resources
Leave a Reply Cancel Reply
All fields are required